Interlocking vs. Standard Grooving Assemblies: What's the Difference?
- Share
- Issue Time
- Jul 24,2025
Summary
difference between interlocking grooves and standard grooves:
1.How They Work: "Locked" vs "Gapped"
2. Performance Showdown
3.How to Choose? Match Your Needs!
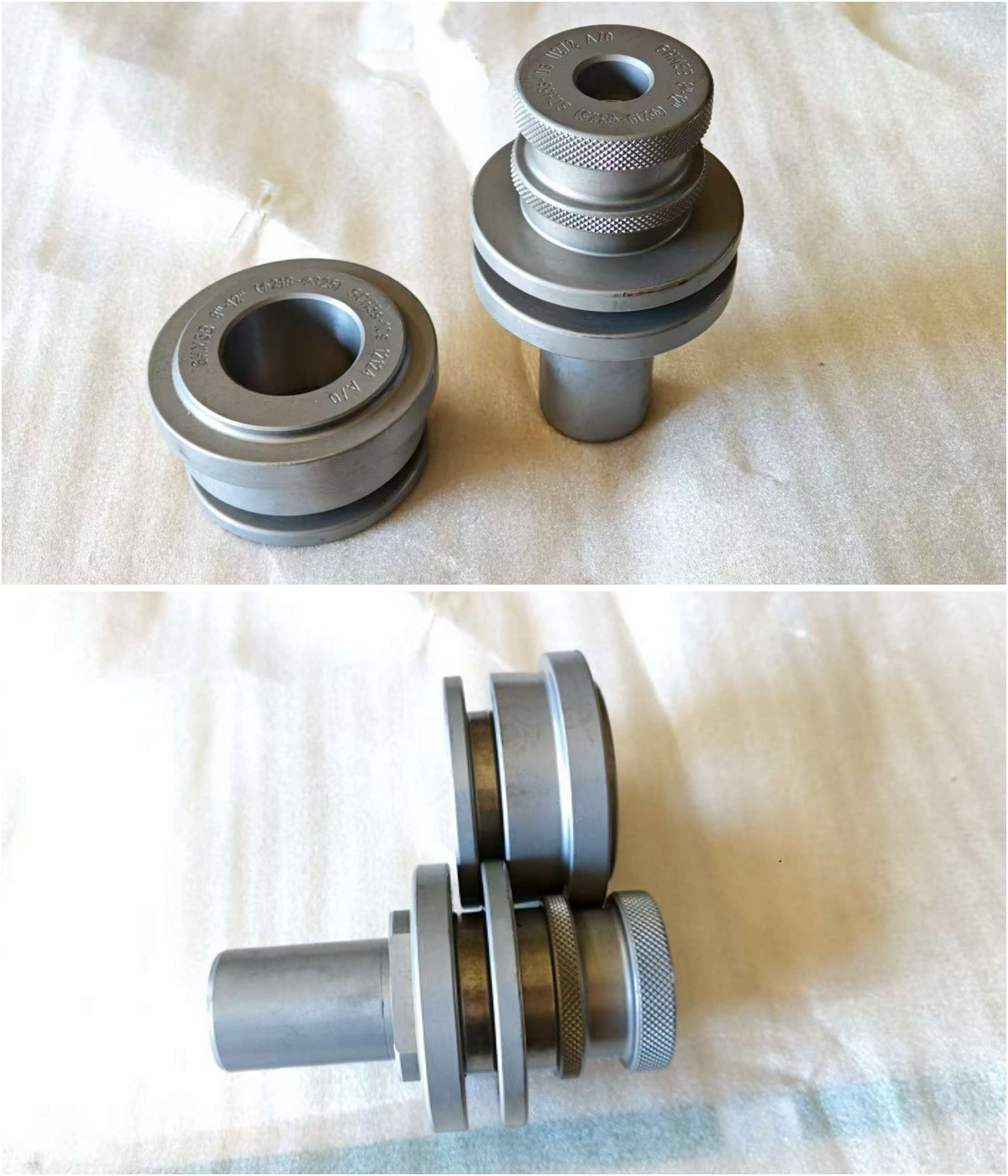
As a Chinese manufacturer with years of expertise in pipe processing equipment, we understand that the core value of roll grooving machine lies in its "efficiency, reliability, and strong adaptability." In practical applications, customers often ask us: "What's the difference between interlocking grooves and standard grooves? Which one should I choose?"
Today, we'll break down the differences between the two in three key aspects—how they work, performance, and best uses—using plain language to help you find the perfect fit for your needs.
1.How They Work: "Locked" vs "Gapped"
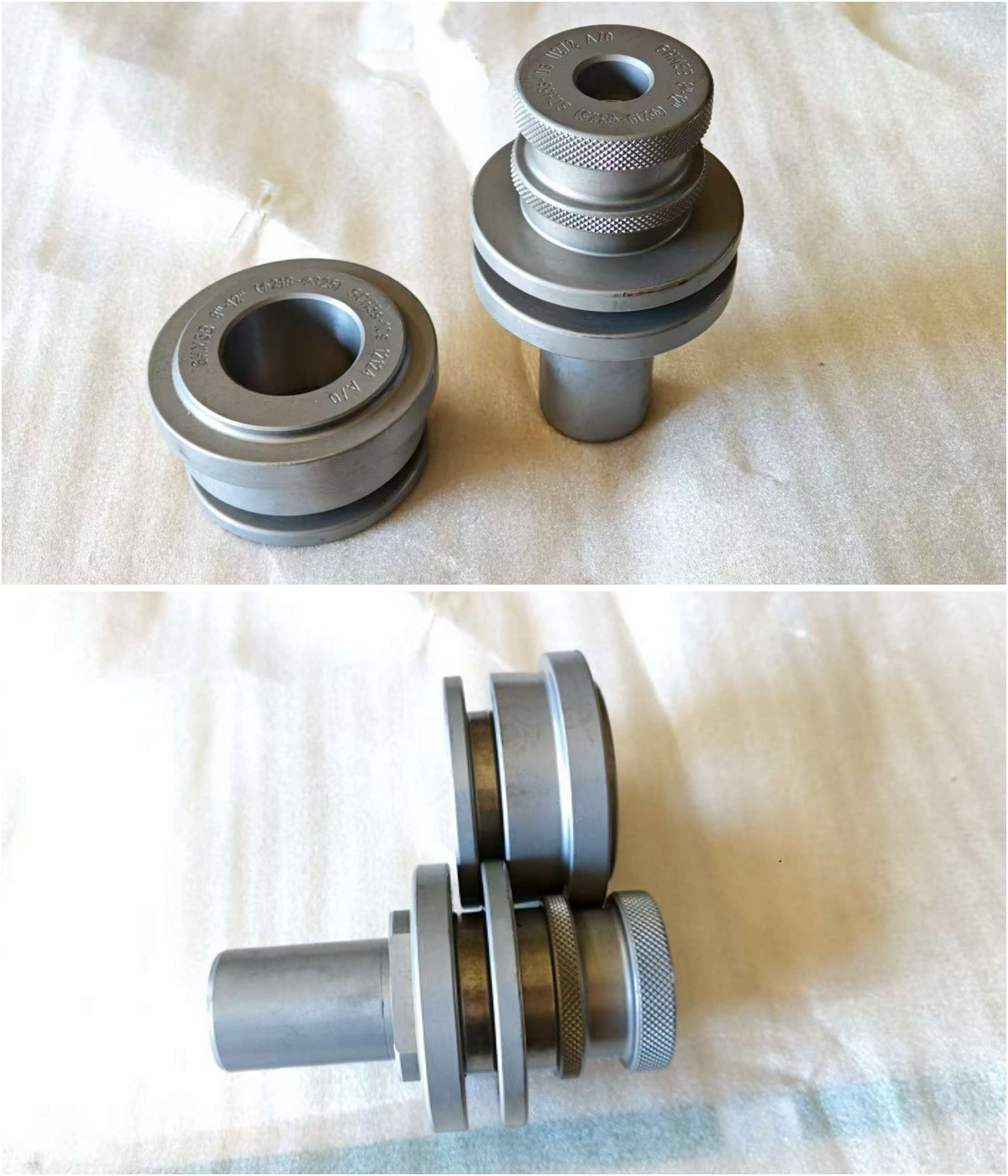
• Interlocking Groove
During rolling, the groove edges form tightly interlocking ridges and recesses (like "gears meshing"). When installed, the pipes self-lock under pressure—no extra seals needed to prevent leaks or slippage.
▶In short: One-piece design, no gaps, resists shifting.
In our grooving machine lineup (e.g., RG-2X, 4X, 6X, 7X, full-auto, AGS series, and pipe groovers), these all use the interlocking design.
• Standard Groove
Features a simple U-shaped or rectangular groove, secured externally by clamps or bolts. Tiny gaps exist between the groove and pipe, requiring gaskets or fasteners for compensation.
▶ In short: Flexible fitting, adjustable tightness, relies on accessories.
Example :
Interlocking grooves work like "Lego blocks"—snap together seamlessly.
Standard grooves are like "drawer slides"—need screws to stay firmly in place.
2. Performance Showdown: Which is Tougher? Which Saves More?
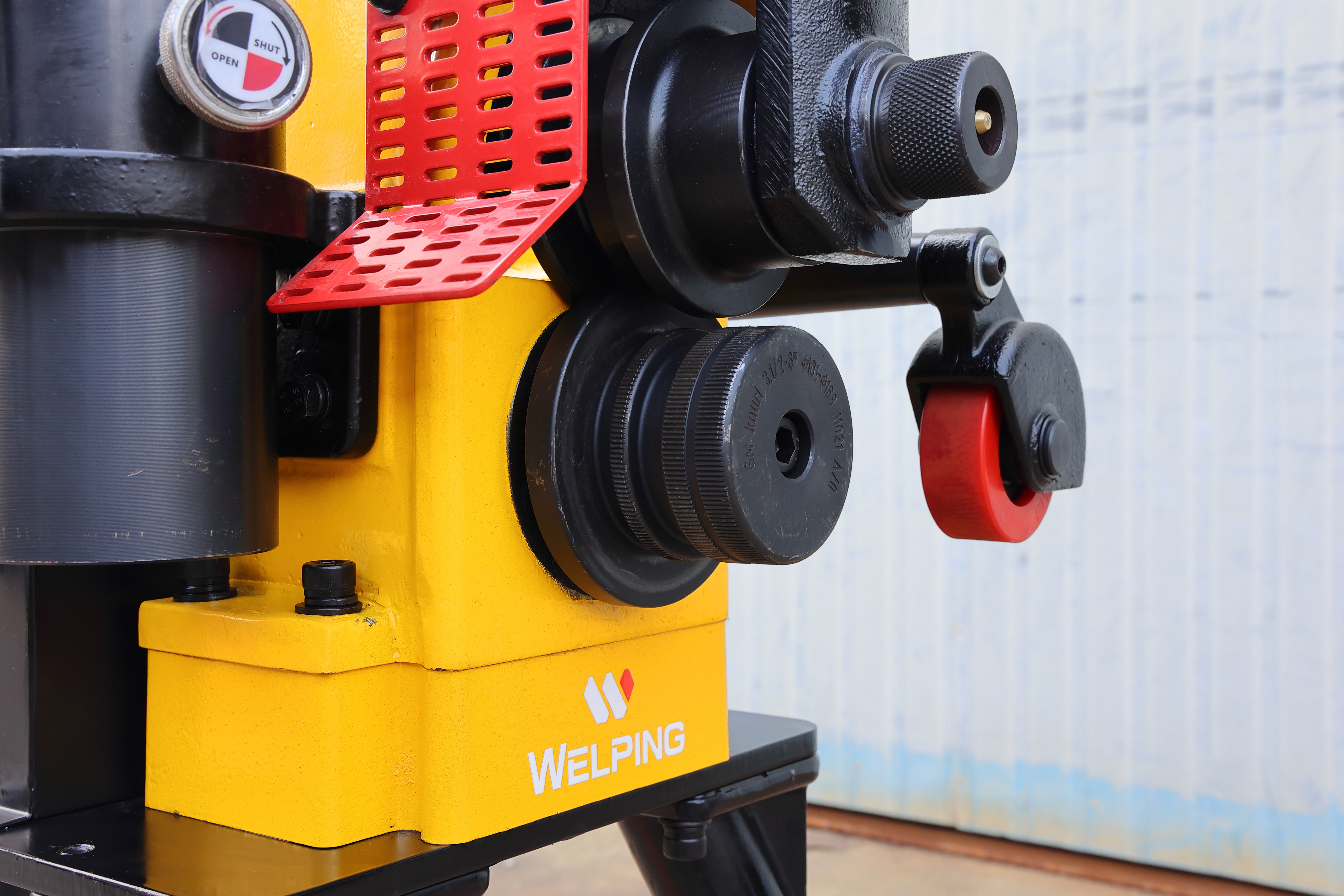
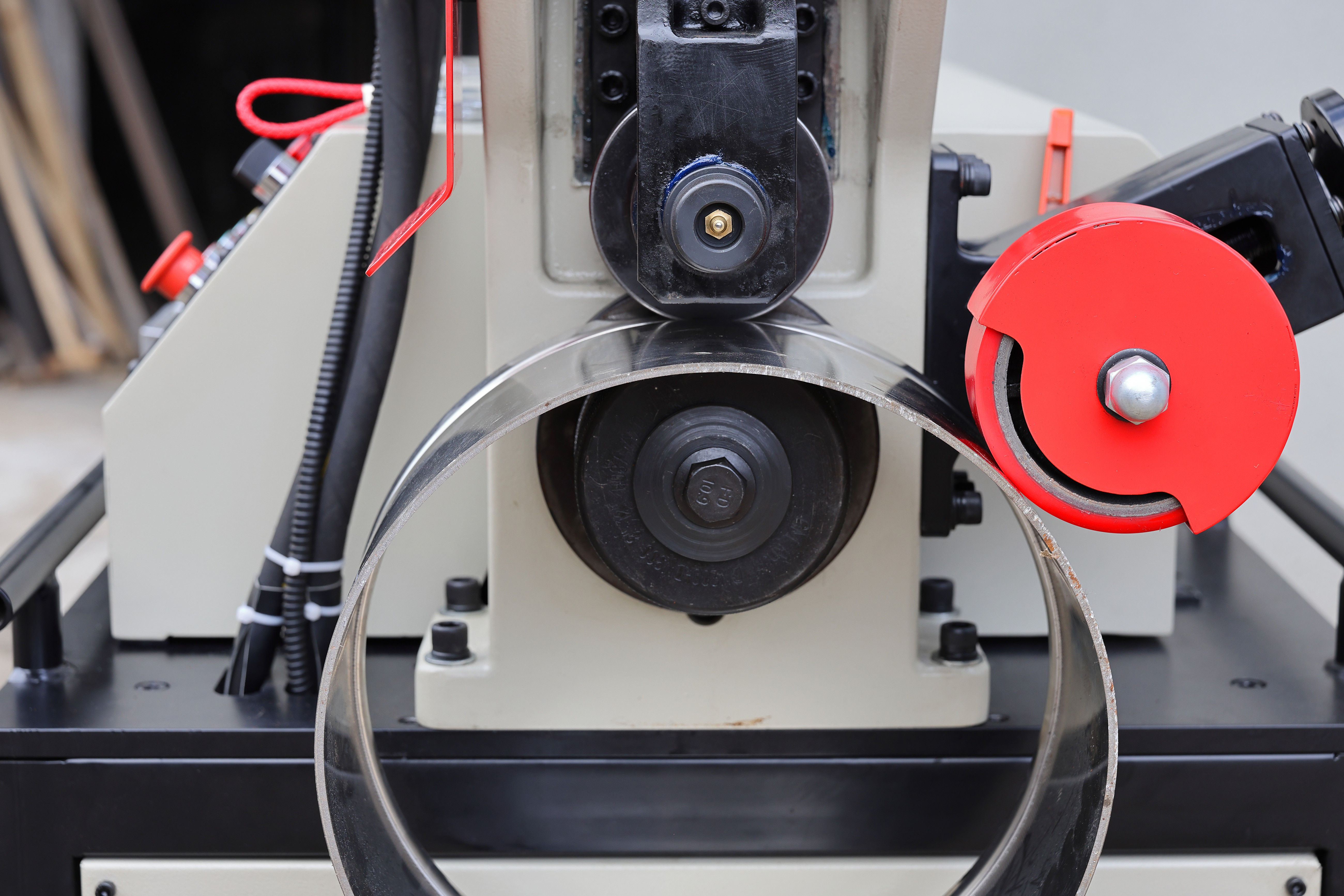
Factor | Interlocking Groove | Standard Groove |
Strength | Extremely high (stress distributed by interlock) | Depends on clamp quality; may loosen under high pressure |
Vibration Resistance | Excellent (won’t separate under vibration) | Requires regular fastener checks |
Sealing | Naturally leak-proof (no-gap design) | Needs extra gaskets |
Cost | Higher per unit (precision molds required) | Lower overall (simpler groove cutting) |
•Hidden Strengths of Interlocking:
✔️ Maintenance-free long-term use—ideal for high-risk applications (chemical, fire protection).
✔️ Eliminates seal degradation, reducing hidden costs.
• Flexibility of Standard Grooves:
✔️ Tolerates minor pipe deformations—faster repairs/replacements.
✔️ Less demanding on groover precision, great for budget projects.
3. How to Choose? Match Your Needs!
• When to Choose Interlocking Groove Best for:
• High-pressure systems (>1.6 MPa)
• High-vibration environments (ships, wind power, heavy machinery)
• Flammable/explosive or harsh conditions (chemical plants, oil/gas)
Why it's better:
1)Better seal: Metal teeth design (like Victaulic Style 07) handles higher pressure (10MPa+) and stops leaks
2)Handles vibration: Locking design keeps pipes from coming loose when shaking
3)Heat/fire resistant: Metal (stainless steel) won't burn or rust like rubber
Common uses:
✔️ Oil/gas pipelines
✔️ High-pressure chemical tanks
✔️ Ship engine piping
✔️ Wind turbine flanges
• When to Choose Standard Groove Best for:
• Low-pressure or no-pressure systems (≤1.6 MPa)
• Temporary or short-term projects (construction sites, temp pipes)
• When you need quick setup or low cost
Why it's better:
1)Costs less: Rubber gaskets are 50% cheaper than metal ones
2)Faster install: No precise alignment needed, good for frequent changes
3)More flexible: Works even if pipes aren't perfectly lined up
Common uses:
✔️AC ventilation ducts
✔️Temporary water pipes at construction sites
✔️Removable pipes in food plants/labs
Pro Tip:
If safety and durability are critical, interlocking's upfront cost pays off long-term. For fast, budget-friendly jobs, standard grooves still deliver.